Abstract
The purpose of this case study is to examine the benefits of HARD-LINE’s TeleOp system as implemented within TVX New Britannia’s underground processes in Snow Lake, Manitoba. The client approached HARD-LINE initially to use the TeleOp system to remotely operate all underground rock breakers from the surface. Expanding operations required additional rock breaker stations, while budgetary constraints would not sustain additional personnel. The article reviews the application of the technology to the client’s underground rock breakers while examining further applications to the client’s tramming and crushing processes. The initial project that HARD-LINE developed and implemented allowed simultaneous remote and local operation of multiple machines by a single operator from a single operator station. This use of the technology would increase operational efficiency by reducing operator transit time between levels and/or machines. It would also facilitate effective and on-budget operational growth incrementally as required by providing an affordable and highly scalable remote operating system. This technology didn’t eliminate jobs but removed the need to hire additional personel in order to process the same amount of material. HARD-LINE’s work with the mine spanned approximately 9 years, as development expanded and needs evolved.
Introduction
The client’s vision for the initial project was to have a fully remote TeleOp-based system to run two existing rock breakers and a third new breaker from a surface-based remote operator station. The objective of HARD-LINE’s initiative was to demonstrate the manner in which TeleOp may affordably increase the efficiency and profitability of a mine. To those ends, HARD-LINE proposed a partially remote system, involving simultaneous local and remote underground breaker operation, thereby substantially reducing development and implementation costs for the project while capitalizing on the capabilities of personnel already operating machinery during each shift.
Challenge
The New Britannia, Snow Lake mine site was a low-grade gold deposit, where operations were required to move and process a substantial amount of material (approximately 2,500 tonnes per day), and get it up to surface and through the mill. When the client purchased the mine, the site was deemed non-economical by previous ownership. This forced the client to find ways to reduce operating costs immediately upon purchasing, without reducing its capacity for moving and processing such large quantities of both ore and waste. Consequently, any system implemented would need to be as efficient and as economical as possible to maintain budget and allow for future growth. The client’s initial vision for an entirely surface-based TeleOp system would have required installation of fiber optic cable in the shaft itself. This was less common in existing mine shafts of the time and correspondingly would have substantially increased the project cost, therefore making it incompatible with the client’s established budget.
Application
In 1997 the client first requested that HARD-LINE build and implement a TeleOp system to allow surface-based remote operation of two existing rock breakers on the 1780 level and a new third rock breaker on the 2300 level. This triple-TeleOp system, however, would have put the project over the established budget. In return, HARD-LINE suggested a single TeleOp system that would allow a single operator to locally work the two 1780 level breakers while remotely operating the third 2300 level breaker from the existing underground operator station. Once accepted, the initial project, from start of build to final implementation, required only two months to complete.
Benefits
During the original project, HARD-LINE’s single-TeleOp system successfully allowed the operator at the 1780 station to locally and remotely operate the required breakers. This eliminated what would have been a lengthy transit time for an operator to be transported as far as the 2300 level. Additionally, this eliminated the need to hire four new employees to operate the 2300 level breaker for each shift in the rotation, a prolonged expense which could not be supported by profits at that time. By extension, this reduced additional employee exposure to the environmental hazards inherent to operating a rock breaker locally.
Following that first phase, additional projects became necessary as the face within the work horizon shifted, requiring more efficient tramming processes to accommodate. A few years after phase one, HARD-LINE’S phase two project consisted of making an RRC (Radio Remote Control) one-person-tram system possible for the mine, allowing one employee load and operate the tram on the 3000 level.
The mine could then divide the usually two-person teams onto separate shifts, once again eliminating the need for out-of-budget additional hiring. When the face eventually shifted again, requiring additional rock breakers, HARD-LINE reconfigured the TeleOp system to then accommodate the continuation of operating the original two rock breakers on level 1780 while also now operating two breakers remotely on the 2300 level.
A few years after phase two, the mine had finished working on the 1780 level and now needed to install a new rock breaker on the 2930 level and a crusher on 3100 level. To those ends, HARD-LINE’s phase three project took all the components that had been used on the 1780 level station and constructed a system which facilitated local operation of the crusher on 3100, along with remote operation of the 2300 breakers which fed into the crusher, and the new third breaker, which itself fed onto the ore and waste pass.
Conclusion
Through all three phases, the TeleOp system and HARD-LINE’s ability to adapt that system as required helped ensure the mine kept its expenses and hiring needs in-line with their growth. With HARD-LINE products managing all of the mine’s material movement, the mine was able to maintain its operating budget through each project, while increasing operational efficiency and safety in its rock breaking and hauling processes. At each phase, the cost of building and implementing each TeleOp project phase was so successfully offset by the savings that each project paid for itself within a few short months of its implementation. Furthermore, the incremental nature of these projects provided job security for mine personnel by keeping operations and the workforce from expanding faster than profits could accommodate. The collective benefits of cost-effective and sustainable growth over time allowed the mine to see profits from its operations for the duration, and demonstrated the ability of the TeleOp system to capably meet the mine’s short- and long-term needs.
Figure 1. TVX Gold – New Britannia mine in Snow Lake, Manitoba
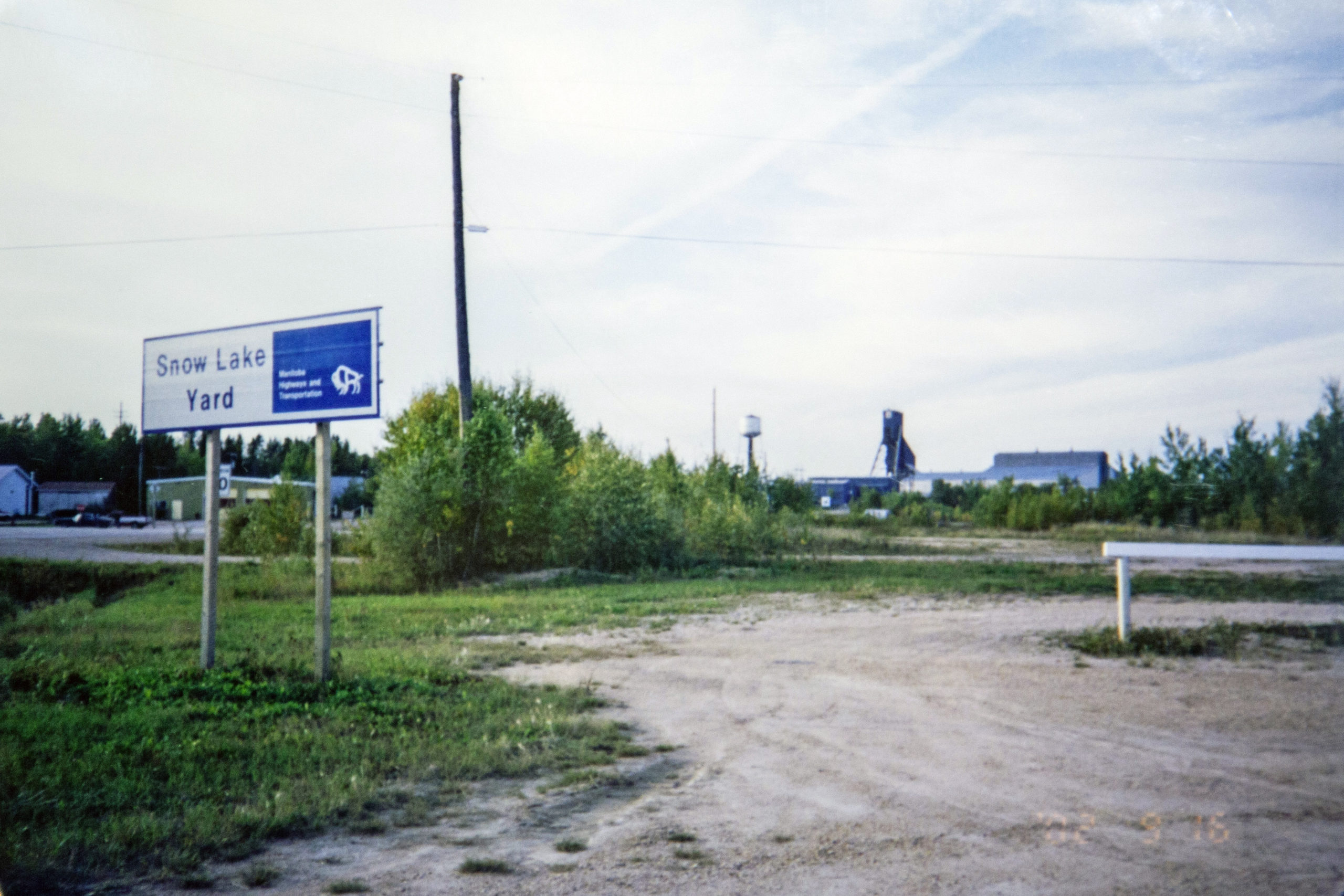
Figure 2. HARD-LINE’s partnership at the mine lasted 9 years
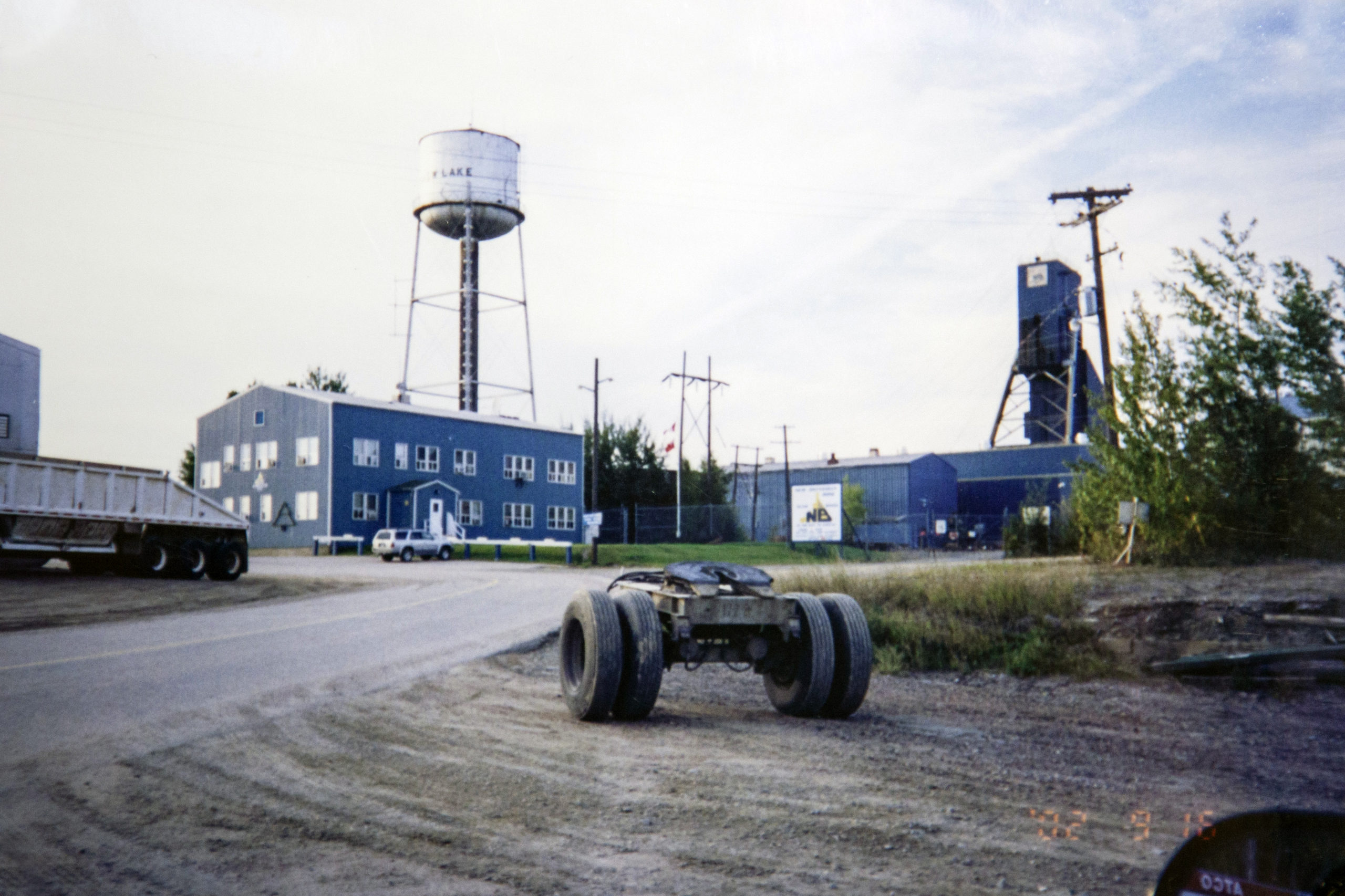
Figure 3. The mine closed in 2005
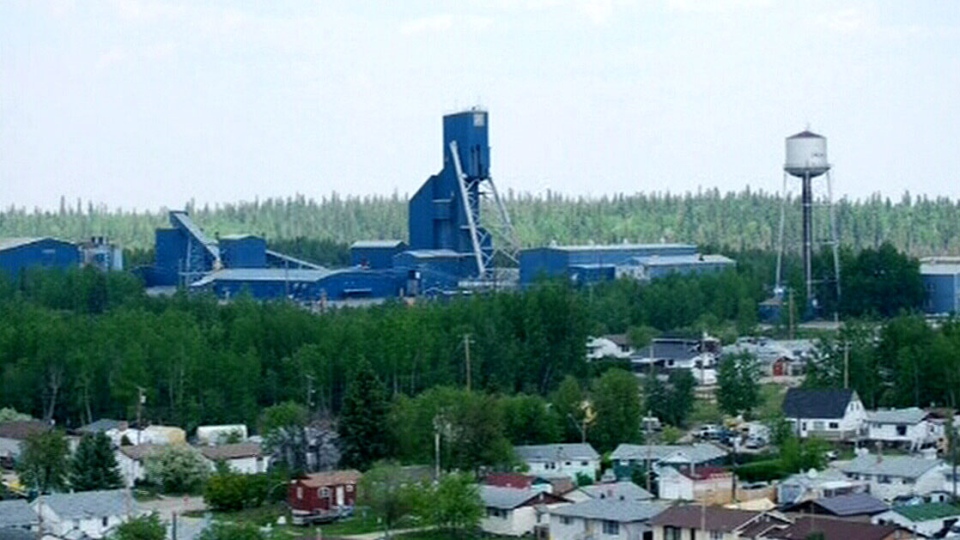